Projects
Priority Programme 2289: (PP 2289 "Hetero-Aggregates")
Projects in Bremen in this Priority Programme:
1) Quantification of the mixing zone and intensification of the mixing process of two nanoparticle producing flames for the design of hetero-contacts
2) DeepMixing – Quantification of the mixing and interfacial heterocharacteristics of nanoparticle aggregates forming in an aerosol mixing zone
Priority Programme 2289, funded by the German Research Foundation (DFG), conducts research on the mixing of disperse systems (particles and powders) as a traditional unit operation of process engineering which is of central importance in various technological areas. It is coordinated in Bremen since October 2021 under the direction of Prof.Dr.-Ing.habil. Lutz Mädler.
Applications of mixed particulate systems range from processing of food, pharmaceutical and chemical substances to material processing and materials engineering. Functional mixing of different particle types (hetero-aggregation) has the potential of creating outstanding new properties of dispersed products, which depend on the mixture composition (for example number of components, concentration, total quantity) and on various secondary process conditions (for example agglomeration, coating).
In this context, a new product property can emerge from the direct contact of different particles (hetero-contact) and thus by the resulting interface between the respective particular components. Many applications have shown that these hetero-contacts are of fundamental importance for specific functional properties. In most cases the new properties result from the transfer of charges, mass, heat, forces, or moments without the need of a chemical reaction of its components. Thus, the quality of such a particulate mixture is directly linked to the contact points and interfaces of different particles and the details of the interaction between its species in contact.
The new property from the contact zone controls the material and product properties of the entire system that is named hetero-contact in the context of the Priority Programme. Direct information about hetero-contact quality (e.g number of contacts, transport properties between different particle types) could therefore be the base for a fundamental description of the new properties of the particle mixture (quality of the mixture and material function). At the same time, the hetero-aggregation process for creating of such hetero-contacts needs to be investigated and controlled.
In the first three years of Priority Programme 2289, the recursive approach dominates, adapting the material system of heteroaggregates to the process measurement technique and the characterisation methods of heteroaggregates and their populations. Special focus is:
- on the establishment of aerosol processes for the defined generation of heteroaggregates, which can also be adapted to process diagnostics for the detection of mixing processes < 1 μm,
- the derivation of particulate sample trains from fast aggregation processes, the establishment of tomographic methods for the characterisation of heteroaggregates with sizes < 1 μm and - their mathematical basis for the description of heteroaggregates as well as
- the establishment of process models and simulations that cover mixing lengths < 1 μm.
The projects in Bremen:
Link to project description "Quantification of the mixing zone and intensification of the mixing process of two nanoparticle producing flames for the design of hetero-contacts"
Contact:Prof.Dr.-Ing.habil.Udo Fritsching
Link to project description "DeepMixing – Quantification of the mixing and interfacial heterocharacteristics of nanoparticle aggregates forming in an aerosol mixing zone"
Contact:Prof.Dr.-Ing. habil.Lutz Mädler und Professor Doctor Andreas Rosenauer
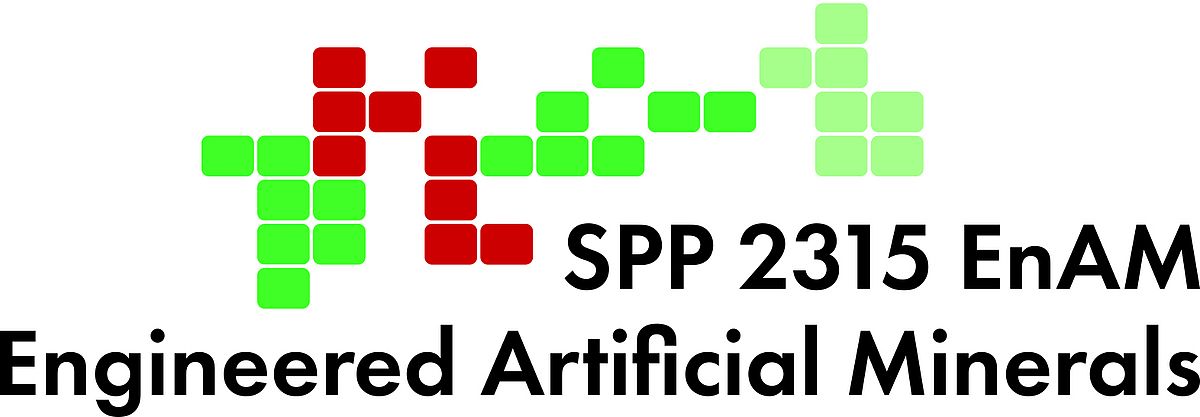
Priority Programme 2315: Engineered Artifical Minerals (EnAM) – a geo-metallurgical tool to recycle critical elements from waste streams (PP 2315 „EnAM")
Project A4 – Exploration of the compositional phase space of metallurgical slag models for a rational design of processes of refractory metal recovery through smelting and recrystallization
The diversity of multicomponent oxides in slag systems offers great advantages in terms of a wide portfolio of crystalline phases that can be recovered from the slag matrix by selective separation. However, the formation of these crystals poses great challenges to a rational process design that ensures (i) sufficient loading of the crystals with elements worth being recovered and (ii) economic viability in terms of process speed and process efficiency.
In this project a rational methodology for the identification and characterization of Engineered Artificial Mineral (EnAM) phases rich in refractory metal elements (especially Ta, Nb, Mo) from metallurgical tin and copper slags will be implemented. The methodology is based on the supervised exploration of the compositional phase space of the slags, in order to screen for, identify and synthesize suitable EnAM phases with the help of slag additives. The leading hypothesis is that the rational and unbiased knowledge of the slag compositional phase space and EnAM formation mechanisms will enable the design processes for the elemental recovery through smelting and recrystallization with high recovery rates and efficiency.
The work towards this hypothesis will be structured in three steps, namely: (1) the fast theoretical screening of a very large number of potential EnAM candidates via database searches and DFT calculations, followed by the synthesis of selected candidates via flame-spray pyrolysis; (2) the design and mechanistic understanding of a laser-induced smelting and recrystallization process for the formation of separable EnAM phases from model slags; (3) the precise and unbiased identification of the EnAM phases at the atomic scale by combining several material characterization methods with a theoretical global-optimization method. The study is expected to provide profound knowledge of the thermodynamics and kinetics of the formation of crystal phases rich in refractory elements from multicomponent systems, which will be transferable to real-world slags and industrial-scale processes.
Contact: Prof. Dr.-Ing. habil. Lutz Mädler, Prof.Dr.-Ing. Lucio Colombi Ciacchi (Universität Bremen)
Further Information about the subproject or the whole project.
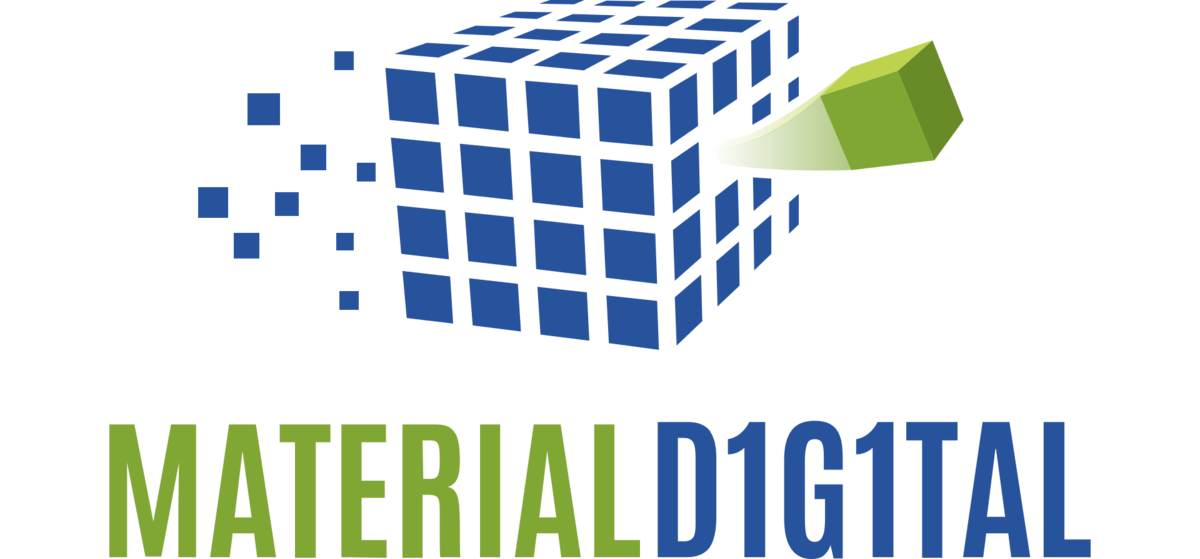
Make material data faster, safer and more accessible: Research knowledge in data platform
MaterialDigital is a joint project of large research institutions, which started in 2019 to establish a digital infrastructure for materials science research data. The "MaterialDigital Innovation Platform", which is funded by the Federal Ministry of Education and Research (BMBF), aims to establish a virtual material data room and thus systematise the handling of material data. Professor Lutz Mädler is a member of the steering committee of MaterialDigital.
The age of digitalisation is already setting new standards for science, as it promises to make the information gained accessible without barriers and thus to accelerate the acquisition of knowledge. Suitable data rooms are able of structuring knowledge to a high degree and thus making it easier to access. In addition they are also supplementing the data treasure with information and using modern statistical methods and generating new knowledge.
In the field of materials science, the innovation platform MaterialDigital is now to perform pioneering work on the digital standardization of materials data and information. In the joint project between the Federal Institute for Materials Research and Testing, the Fraunhofer Institute for Mechanics of Materials IWM, the Helmholtz Association, the Leibniz Institute for Materials Engineering - IWT and the Max Planck Institute for Iron Research, the project partners will develop initial approaches to master the complex data management required for this. To this end, contributions from all sectors involved in materials development and processing will be brought together: industry, non-university research institutions and universities.
Contact: Prof. Dr.-Ing.habil. Lutz Mädler
To the MaterialDigital platform
Research Unit FOR 2688: Instabilities, Bifurcation and Migration in Pulsatile Flows
Dynamics and Instabilities of particle-laden pulsatile flows in complex pipe geometries
The research group FOR 2688, funded by the German Research Foundation (DFG), aims at gaining a fundamental understanding of pulsatile flows.
In engineering (for example fluid transport by pumping) and in biological systems (for example blood flow) pulsatile flows are common, but little is known about how the oscillating part of the volume flux influences the flow dynamics.
We tackle this question in an interdisciplinary team of engineers, physicists and physicians. Our research covers basics of flow instabilities and particle migration, to the complex motion and deformations of red blood cells. The methods range from precision experiments and particle-resolved simulations, to the in-vivo imaging of individual blood cells. The long-term goal of our research is to lay the hydrodynamic foundations for a better understanding, prevention and treatment of vascular diseases and strokes.
The research group FOR 2688 consists of five experimental and three numerical subprojects within Germany, Switzerland and Austria. Dr. Kerstin Avila is a young scientist and is for the first time principal investigator of a DFG project. Professor Christian Wagner from Saarland University is the spokesperson of the FOR 2688.
Link to the DFG of the subproject „Dynamics and Instabilities of particle-laden pulsatile flows in complex pipe geometries“
Link to the homepage of the research unit FOR 2688
Contact: Dr. rer. nat. Kerstin Avila
ReSuNiCo - basic research for process understanding of single droplets
Inverted Reactive Spray Processes for Sulphide/Nitride High Surface Area Electrode Coatings
The ERC Advanced Grant was awarded to Professor Lutz Mädler in April 2018. Within this project new reactor concepts for reactive spraying are developed. This technology can be used to produce customized materials and surfaces - for example, flexible electronic and catalytic coatings that are used to measure exhaust gases. Experiments are conducted on tiny individual droplets that are only slightly larger than the diameter of a hair. Research on these isolated droplets is inexpensive and allows a large number of rapid experiments.
With the experiments on single droplets, the research group is moving into dimensions that are no longer visible to the naked eye. Nevertheless, one of the important goals of the project, which is funded by the European Research Council, is to transfer the knowledge gained to larger scales and to move towards industrial applicability.
Contact:Prof. Dr.-Ing. habil. Lutz Mädler
to the film about the research
Priority Programme 2045: Highly specific and multidimensional fractionation of fine particle systemes with technical relevance (SPP 2045 "MehrDimPart")
Selective Particle Fractionation in Multi-Parameter Potential Fields / Multi-Field Fractionation (M-FF)
Development of separation methods and processes for the fractionation of highly specific fine particle systems (< 10 μm) with multidimensional property distributions in industrially relevant mass flows.
In the Priority Programme 2045 funded by the German Research Foundation (DFG), 24 sub-projects are being carried out with the aim of further developing existing particle technology processes and identifying and implementing new approaches in order to solve the separation tasks of the present and, above all, of the future.
In line with the development of demand in the processing industry, the requirements for primary and secondary raw materials are becoming continuously higher. Increasingly purer, finer and more specific particle systems must be provided in order to guarantee the required quality of the end product. Since many of the established separation processes in the field of finest particles (< 10 μm) are losing much of their specificity, alternative approaches must be developed. This is done in the subprojects located throughout Germany under the coordination of the Institute of Mechanical Process Engineering of the Technische Universität Bergakademie Freiberg.
Due to excellent approaches to solve the presented problem, the Universität Bremen could contribute 3 subprojects.
The Particles and Process Engineering group of the Universität Bremen and the Leibniz-Institute for Materials Engineering IWT are conveying the project B4: "Selective Particle Fractionation in Multi-Parameter Potential Fields / Multi-Field Fractionation (M-FF)". In this project, particles from an aerosol are separated into fractions by means of superposition of acoustically resonant and electric fields, depending on the material parameters of the specific particles.
Contact:Prof. Dr.-Ing habil.Udo Fritsching
Further information about the subproject or the whole project
A publication about the project can be found in Chemie Ingenieur Technik or the link:
Priority Programm 2006: Compositionally Complex Alloys – High Entropy Alloys (SPP 2006 CCA-HEA)
Particle-strengthened Compositionally Complex Alloys – interlinking powder synthesis, additive manufacturing, microstructure evolution and deformation mechanisms
Complex alloys, such as high-entropy alloys, are a relatively new class of metallic alloys that are fundamentally different from conventional alloys, have excellent mechanical properties and whose phenomena are hardly understood with classical materials knowledge. The SPP aims at a fundamental understanding of the characteristic structural and microstructural features of these materials in order to make them attractive for future applications.
In the project "Particle Reinforced Compositionally Complex Alloys" it is investigated whether the mechanism of particle reinforcement in Compositionally Complex Alloys (CCA) can be used to achieve outstanding mechanical properties. Although it is known that nanoscale particles are present in many CCA, their precipitation mechanism, kinetics and influence on the mechanisms of plastic deformation are still largely unknown. In order to systematically expand the concept of CCA to specifically particle reinforced CCA (p-CCA) and to penetrate it from a materials science perspective, structural analyses down to the atomic length scale are required. The p-CCA samples are produced by means of a flexible powder metallurgical process, which includes melting of the alloys, gas nozzles and additive manufacturing by laser beam melting (L-PBF). This allows us to take advantage of the benefits of the SLM process, especially the rapid solidification to avoid segregation. The process can only be run stable if the powders meet requirements with regard to size distribution, morphology and flowability. Powder technology is therefore a central aspect of the project, in which the use of flow-improving additives in particular is also being investigated.
Further information about PP 2006
Kontakt: Dr.-Ing.Volker Uhlenwinkel
Priority Programme 1980: Nanoparticle Synthesis in Spray Flames SpraySyn: Measurement, Simulation, Processes (SPP 1980 SpraySyn)
Precursor release in nanoparticle producing spray flames: Single droplet investigation of multicomponent mass transfer
and
Process analysis and control of atomizing and mixing zones in spray flames
The aim of the priority program funded by the German Research Foundation is to achieve a fundamental understanding and theoretical modeling of the entire flame spraying process in an interdisciplinary network. The focus is on the development and application of specific in-situ analytical methods, the establishment of chemical mechanisms through basic kinetic experiments and theoretical calculations and a comprehensive simulation of the process chain precursor solution - spray - flame - particle, adapted to the problem. The development and use of a standard experiment ("SpraySyn Standard Burner"), which is to be established internationally as a reference experiment with a comprehensive validation data set, plays a key role. In the long term, it will serve as an anchor point for research and development of particle synthesis in spray flames. The SPP 1980 is coordinated at the University of Duisburg-Essen. Professor Lutz Mädler is one of the three organizers of this SPP.
Link to the project description "Precursor release in nanoparticle producing spray flames: Single droplet investigation of multicomponent mass transfer"
Contact:Prof. Dr.-Ing. habil.Lutz Mädler
Link to the project description "Process analysis and control of atomization and mixing zones in spray flames
Contact:Prof. Dr.-Ing.habil. Udo Fritsching
Collaborative Reaseach Center 1232 - From colored states to evolutionary structural materials
The Collaborative Research Centre 1232 "Farbige Zustände" at the University of Bremen was a research association spanning several institutes and departments and expired on March, 30th 2021.
The spokesperson was Prof. Dr.-Ing.habil. Lutz Mädler.
The SFB developed a novel experimental method of materials development. The overall aim was the efficient and focused identification of compositions and process chains which result in a specific performance profile of the material. More than 50 scientists from the fields of production engineering, process engineering, materials engineering, mathematics and computer science conducted interdisciplinary research.
Contact:Prof. Dr.-Ing.habil. Lutz Mädler
Priority Programme 1934:Dispersity, structure and phase changes of proteins and bio agglomerates in biotechnological processes (SPP 1934 DiSPBiotech)
Impact and control of mechanical stress on protein structures during formulation in premix-emulsification
The aim of the project, which is funded by the German Research Foundation, is to investigate dispersity, structure and phase changes of proteins and biological agglomerates in biotechnological processes. One subproject is the characterization of the mechanical stress (stress-residence time behavior) of proteins and protein agglomerates and the effect on protein structure and functionality in downstream processing using the example of the premix emulsification process. Process-induced protein structural changes will be characterized by comparative numerical (CFD simulation and molecular dynamics) and instrumental-analytical (FTIR, drop shape) investigations. The derivation of mechanical stress and damage models for proteins and bioagglomerates during membrane emulsification will enable the targeted control of mechanical processes. For this purpose, an interdisciplinary network is available within the SPP. Finally, the storage stability of protein-based emulsions and thus the product quality can be positively influenced by adapted stress-reduced processing. The applicants are Professor Udo Fritsching from the Partikles & Process Engineering Group and Professor Stefan Drusch from the TU Berlin.
Contact:Prof. Dr.-Ing.habil. Udo Fritsching
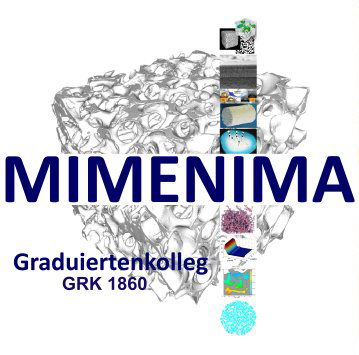
Research Training Group 1860: Micro-, Meso- and Macroporous Nonmetallic Materials: Fundamentals and Applications (RTG 1860 MIMENIMA)
Transport, Separation, and Mixing of Complex Multiphase Fluids in Pores sand Porous Membranes with Varying Surface Activities (P07/03)
and
Simulation of Structural Changes of Mesoporous Films and Layers during Liquid Infiltration and Drying (P08/03)
The overall research idea of the MIMENIMA Research Training Group, which is funded by the German Research Foundation (DFG), is the conditioning of novel, porous ceramic structures and their surfaces for use in important areas of energy, environmental, process and space technology. For this purpose, the research training group addresses five research areas: material development, structure & process analysis, basic experiments on mass transport in porous media, modelling & simulation and special applications.
Currently 11 projects with different topics are working on the development of new porous materials or processes with porous materials, as well as methods for the characterization of porous materials.
There are two projects carried out by the Particle and Process Engineering group of the University of Bremen and the Leibniz-Institute for Materials Engineering – IWT. One involves the investigation of rheologically complex multiphase fluids and the emulsification process both through experimental as well as computational studies. The goal is to develop models for industry relevant emulsions in order to predict the experimentally observed pressure drops and droplet size distributions and determine the shear stresses exerted under the conditions these are possible. The other project deals with the investigation of the physiochemical properties of mesoporous films built up from nanoparticle aggregates and agglomerates as well as developing models for the underlying mechanisms. Understanding the fundamental mechanisms that govern the structural changes in mesoporous films during liquid imbibition and drying has important applications in electrochemical characterisation, production of polymer hybrid materials and performance of liquid electrolyte cells.
Link to project (P07/03) „Transport, Separation, and Mixing of Complex Multiphase Fluids in Pores sand Porous Membranes with Varying Surface Activities“.
Contact:Prof. Dr.-Ing.habil. Udo Fritsching
Link to project (P08/03) „Simulation of Structural Changes of Mesoporous Films and Layers during Liquid Infiltration and Drying“.
Contact:Prof. Dr.-Ing. habil. Lutz Mädler
Further information about MIMENIMA and the projects within the graduate school